Cost Reduction is crucial for manufacturing companies to stay ahead of the competition.
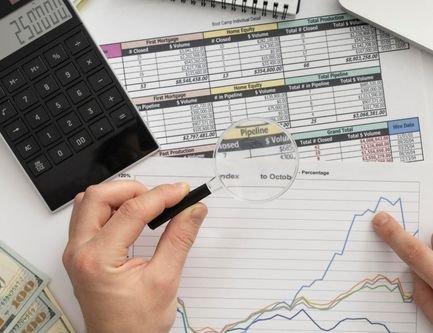
In today’s competitive business environment, cost reduction is crucial for manufacturing companies to stay ahead of the competition. Year over year, customers demand price reductions, while vendors demand price raises. Additionally, employees demand salary raises, and manufacturing companies face other increasing costs such as raw materials, energy, and transportation costs. All of these factors make cost reduction essential for the long-term success of any manufacturing company.
Our team of experts offers a range of cost reduction services that can help manufacturing companies achieve their cost-saving goals.
Traditional Cost Accounting may result in bankruptcy many a times.
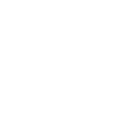
Measuring Various Costs
Our first step is to measure the various costs that manufacturing companies incur. By analyzing the cost structure, we identify the areas that need improvement and take necessary action to reduce systems costs just not the local cost center wise costs etc. We use advanced analytical tools and techniques like Throughput Accounting to measure and track costs, which enables us to provide our clients with valuable insights that help them make informed decisions.
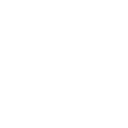
Developing Cost Reduction Strategy
Our team works closely with our clients to develop a customized plan that aligns with their business objectives. We help our clients identify various cost-saving opportunities and prioritize them based on their impact on the business. By implementing our cost reduction strategies, manufacturing companies can achieve significant cost savings in the tune of 3-7 % of their current turnover through application of internationally proven Lean and TOC approaches .
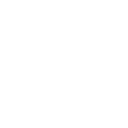
Better Working Team and Organization Structure
We help our clients develop a better working team and organization structure, which leads to improve efficiency and productivity. Our team works with the client to identify and eliminate any bottlenecks that may be affecting productivity, resulting in cost savings.
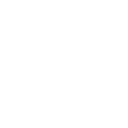
Implementing Theory of Constraints
Our experts also implement the Theory of Constraints, which is a powerful management tool used to identify and eliminate bottlenecks in the production process. By identifying and resolving bottlenecks, we help our clients improve the overall efficiency of their operations, resulting in significant cost savings and doubled profits*generally.

Standardizing Critical Processes
We help our clients standardize critical processes to eliminate any inefficiencies and reduce costs. By standardizing the process, we reduce variability and improve quality, which leads to cost savings.

Reducing Unwanted Inventories
Our team works closely with the client to identify and reduce unwanted inventories, which can tie up valuable resources and lead to unnecessary costs. By reducing inventories, manufacturing companies can improve their cash flow and reduce storage costs and capital expenditure.

Implementing 5S Methodology
We also implement the 5S methodology to improve efficiency and productivity. By implementing this methodology, we help our clients eliminate waste, reduce costs, and improve quality.
Get in touch to explore how we can reduce the Costs Significantly!
