Operational excellence is essential for any organization looking to increase profits and succeed long-term.
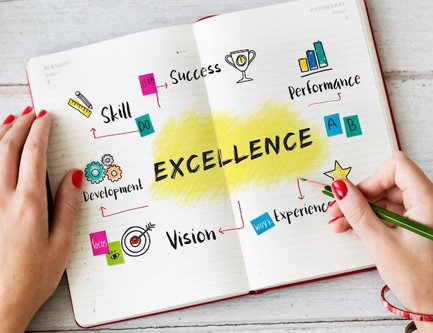
Lean Six Sigma is a methodology that has been proven to provide a competitive edge and create a more efficient, profitable organization. Its success has been demonstrated by the transformation of Toyota (under leadership of Taichi Ohno) and GE under Jack Welch’s leadership, which emphasizes the impact of operational excellence.
We understand the importance of operational excellence and offer a range of services to help businesses achieve it.
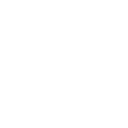
Identifying and reducing 8 Lean wastes
We can help you identify and reduce the 8 Lean wastes: Defects, Overproduction, Waiting, Not utilized Talent, Transportation, Inventory, Unnecessary Motion, Extra -Processing, and. Ultimately reducing the biggest waste of time i.e. “WAITING” and increasing the ROTI [Return On Time Invested]. The waste mapping is understood through Value Stream Mapping.
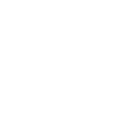
Customized roadmap using the DMAIC methodology
We help you create a roadmap that is tailored to your specific needs and handhold you through the implementation of Lean Six Sigma to ensure success using the DMAIC methodology (Define → Measure → Analyse → Improve → Control)
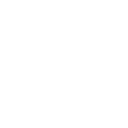
Handholding implementation of tools
We can help you implement world class Lean tools, such as Value Stream Mapping (VSM), Just-in-Time (JIT), Inventory reduction / Management, 5S ,Kaizen, Visual Control , Total Productive Maintenance (TPM), Total Quality Management (TQM), Control Plan , SOP’s , FMEA , Single-Minute Exchange of Die (SMED), and Poka Yoke etc.
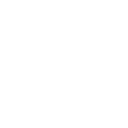
Creating a problem-solving culture
We can help you create a problem-solving culture by introducing Systematic Problem Solving tools such as Corrective Action Preventive Action (CAPA), 8-Disciplines (8D) model, A4 problem solving, 5-Why analysis, Pareto Analysis, and more and very
Holistic 8-“I” model.
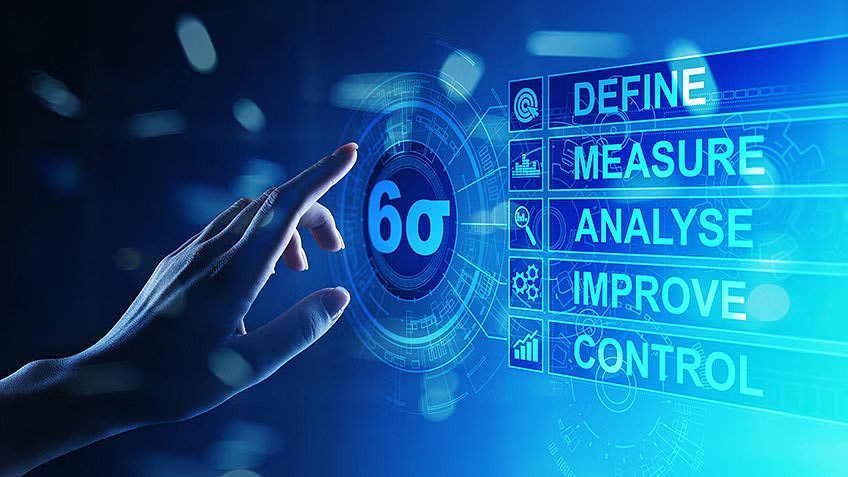